Spherical washers are specialized components designed to enhance performance and reliability in high-load applications. Their unique geometry allows for better alignment and load distribution, making them ideal for various industries, including construction, automotive, aerospace, heavy machinery, etc. This article explores the advantages, applications, and selection criteria for spherical washers in high-load environments.
What are Spherical Washers?
Spherical washers consist of a convex surface on one side and a concave surface on the other. This design allows the washers to self-align with the surface of the fastener, compensating for angular misalignments and uneven surfaces. As a result, they distribute loads more evenly across the assembly, minimizing the risk of stress concentrations that can lead to failure.
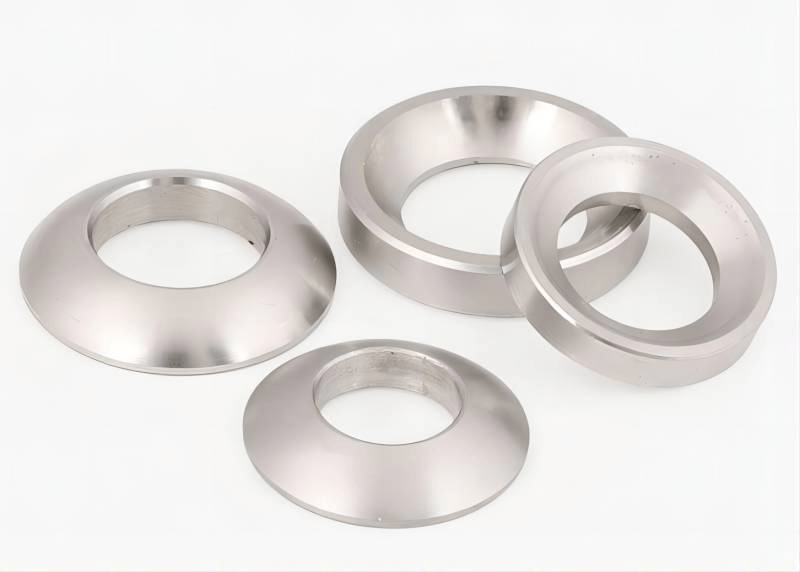
Advantages of Spherical Washers in High-load Applications
1. Compensation for Angular Misalignment
Spherical washers are designed to accommodate angular misalignments between fasteners and the surfaces they connect. This feature allows them to adapt to slight deviations without compromising load distribution. By ensuring that the load is applied uniformly, spherical washers help maintain the integrity of the joint, even in applications where precise alignment cannot be guaranteed.
2. Even Load Distribution
The geometry of spherical washers facilitates the even distribution of load across the contact surfaces. This reduces the risk of localized stress concentrations that can lead to fatigue and eventual failure. In high-load environments, maintaining an even load is crucial for the longevity of both the fasteners and the components they secure.
3. Increased Durability
By minimizing stress concentrations and wear on fasteners, spherical washers enhance the overall durability of the assembly. This is particularly important in high-load applications where components are subjected to repeated stress cycles. The increased durability translates to longer service life and reduced maintenance requirements.
4. Enhanced Vibration Resistance
High-load applications often involve vibrations that can loosen fasteners over time. Spherical washers help maintain a secure fit, reducing the likelihood of loosening due to vibration. This vibration resistance is critical in applications such as automotive engines, heavy machinery, and structural components, where safety and reliability are paramount.
5. Reduction of Stress Concentrations
Spherical washers effectively spread the load over a larger surface area, which minimizes localized stresses. This is particularly beneficial in high-load applications where materials can be prone to failure due to stress concentrations. By preventing these high-stress points, spherical washers enhance the structural integrity of the joint.
6. Simplified Installation and Assembly
Spherical washers simplify the installation process by allowing for some degree of misalignment between the bolt and the clamping surface. This feature reduces the need for precise alignment during assembly, making the installation process quicker and more efficient, especially in challenging environments.
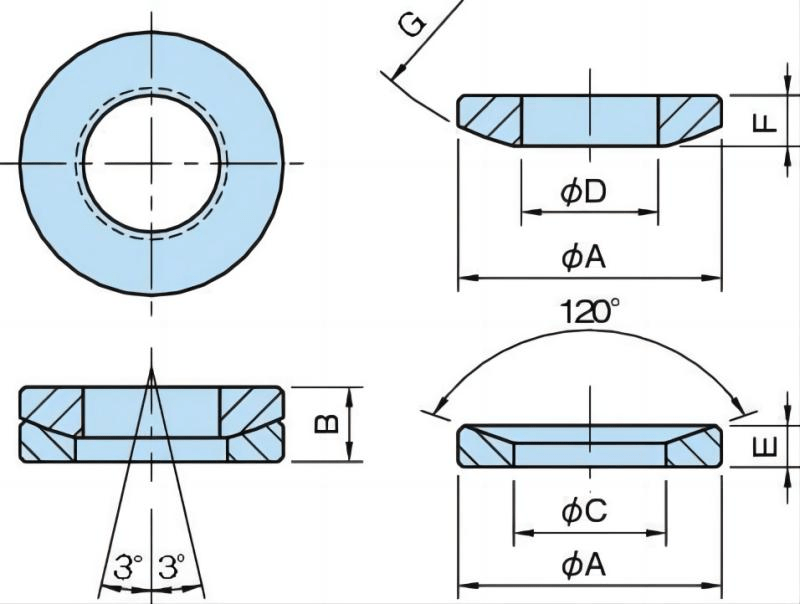
7. Cost-Effectiveness
Although spherical washers may have a higher upfront cost compared to standard washers, their ability to enhance performance, reduce maintenance, and extend service life can result in lower overall costs in high-load applications. This cost-effectiveness is especially significant in industries where downtime can be expensive.
8. Improved Safety and Reliability
In high-load applications, ensuring the safety and reliability of connections is critical. Spherical washers enhance the performance of fastening systems, contributing to safer and more dependable operations. This is vital in industries like aerospace and construction, where failure can have catastrophic consequences.
Common High-load Applications of Spherical Washers
This chart provides a clear overview of the various high-load applications of spherical washers and their significance in each context.
Application | Description |
Heavy Machinery | Used in construction and mining equipment to maintain secure bolted connections under extreme loads. |
Aerospace | Ensures structural integrity in aircraft components, accommodating dynamic loads and misalignment. |
Automotive | Enhances reliability in critical assemblies such as engines and suspension systems under high stress. |
Bridge Construction | Compensates for thermal expansion and load changes, maintaining secure joints in large structures. |
Renewable Energy (Wind Turbines) | Maintains connections in turbines subject to varying loads and environmental conditions. |
Industrial Equipment | Used in heavy-duty machinery to secure components that experience constant vibration and heavy loads. |
Marine Applications | Ensures structural stability in vessels where dynamic forces and misalignment are common. |
Railway Systems | Maintains track integrity and connections in rail systems subjected to heavy and dynamic loads. |
Oil and Gas Industry | Used in drilling and extraction equipment to ensure secure connections under high-pressure conditions. |
Construction Fasteners | Ensures effective load transfer and alignment in structural frameworks and connections. |
Materials Used for Spherical Washers in High-load Applications
To withstand the demands of high-load applications, spherical washers are typically made from high-strength materials.
- Hardened Steel: Ideal for heavy-duty applications due to its durability and load-bearing capacity.
- Stainless Steel: Offers corrosion resistance, making it suitable for harsh environments such as marine or chemical processing industries.
- Brass and Bronze: Often used for applications requiring lower friction or where non-magnetic properties are necessary.
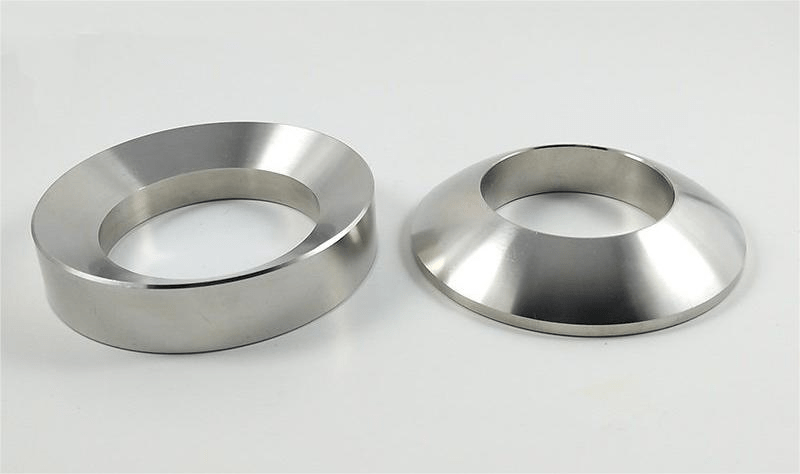
Key Factors to Consider for Selecting the Right Spherical Washer for High-load Applications
This chart provides a concise overview of the essential factors to consider when selecting spherical washers for high-load applications.
Factor | Description | Considerations |
Load Capacity | Maximum load the washer can handle without failure. | Ensure the washer accommodates expected loads, including potential overloads. |
Material Compatibility | The material of the washer affecting durability and environmental resistance. | Choose materials (e.g., hardened steel, stainless steel) compatible with the operational environment. |
Temperature Resistance | Ability to maintain performance under varying temperature conditions. | Assess the operating temperature range; ensure the washer withstands these conditions. |
Degree of Misalignment Accommodation | Extent to which the washer compensates for misalignment between surfaces. | Evaluate expected angular misalignment; select washers that effectively accommodate it. |
Thickness and Size | Dimensions affecting load distribution and fit within the assembly. | Ensure thickness and diameter are suitable for fasteners and assembly design. |
Vibration Resistance | Ability to maintain performance under vibrational stresses. | Select washers designed to provide a secure fit and minimize loosening in vibration-prone applications. |
Surface Finish | Texture and treatment affecting friction and wear characteristics. | Consider surface finish based on application needs, such as low friction or enhanced grip. |
Environmental Conditions | Factors like moisture and chemicals that could affect performance. | Choose washers that withstand specific environmental challenges for longevity and reliability. |
Cost vs. Performance | Balance between initial cost and long-term performance benefits. | Evaluate cost-effectiveness; consider that high-quality washers may reduce maintenance costs. |
Manufacturer Specifications and Standards | Compliance with industry standards that dictate performance and quality. | Ensure washers meet relevant standards for assurance of quality and reliability in applications. |
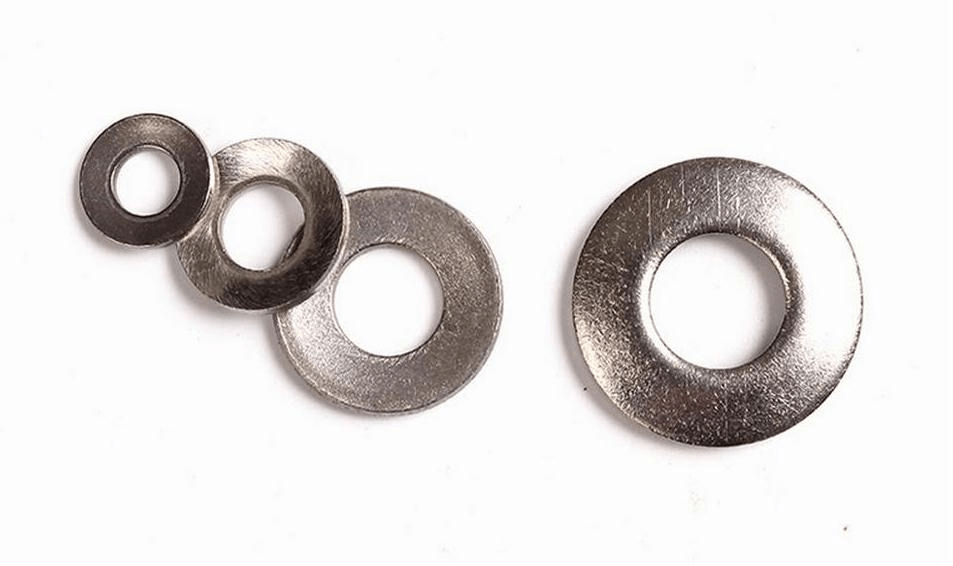
In summary, spherical washers provides enhanced alignment, load distribution and durability, making them essential in high-load applications. Their unique design makes them invaluable in industries where reliability is critical. Through understanding their advantages and selecting the appropriate materials and specifications, engineers and designers can significantly improve the performance and longevity of their fastening systems.