Rivet nuts, also known as thread inserts, are essential fasteners used to create strong, durable threads in thin materials like sheet metal. Traditionally, their installation required manual tools, which could be time-consuming and labor-intensive, particularly in high-volume industrial applications. However, recent innovations in rivet nut installation tools have significantly improved efficiency, precision, and ease of use.
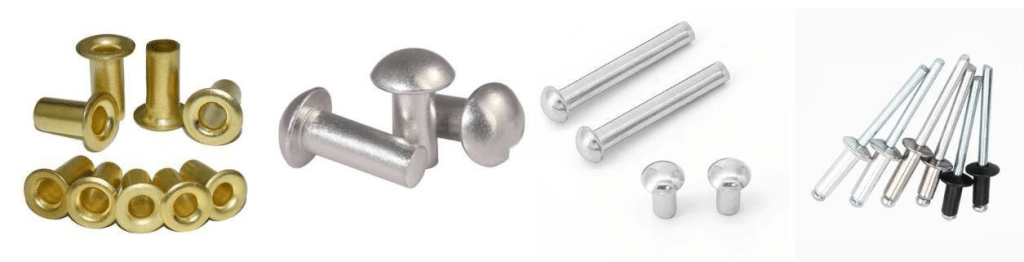
What are Traditional Commonly Used Rivet Nut Installation Tools?
This chart summarizes traditional rivet nut installation tools, highlighting their applications and limitations, which can guide users in selecting the appropriate tool for efficient rivet nut installation.
Tool Type | Description | Applications | Limitations |
Basic Hand Rivet Nut Tool | Simple lever-operated tool for compressing and setting rivet nuts manually. | Home repairs, hobby projects, and small-scale applications. | Labor-intensive; not suitable for high-volume applications. |
Lever-Action Rivet Nut Tool | Manual tool with longer handles for increased leverage, allowing easier installation. | Medium-scale installations where moderate force is needed. | Still requires significant manual effort; can cause operator fatigue. |
Spin-Spin Rivet Nut Tool | Manually operated tool that tightens the rivet nut by spinning the mandrel. | Low-force applications, such as thin sheet metal. | Limited effectiveness; may not provide consistent torque and requires careful handling. |
Threaded Insert Tool | Uses a threaded mandrel to screw in the rivet nut before applying pressure to deform it. | Repairs in automotive and electronic applications. | Slower installation process; requires precise alignment and may not work with all materials. |
Wrench-Type Rivet Nut Tool | Combines a wrench with a mandrel for manual tightening of rivet nuts. | Light-duty tasks and general assembly work. | Labor-intensive; can be cumbersome in tight spaces. |
Plier-Style Rivet Nut Tool | A plier-like tool that squeezes to install rivet nuts, ideal for quick jobs. | Quick installations in soft materials, such as plastic or thin metal. | Limited leverage and grip; may struggle with larger or thicker materials. |
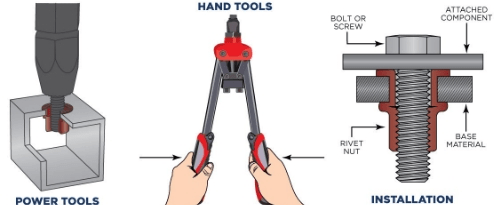
Latest Advancements in Rivet Nut Installation Tools
1. Ergonomically Designed Manual Tools
While manual rivet nut tools have been around for years, newer designs focus on reducing operator fatigue and increasing efficiency. Innovations such as ergonomic handles and better grip designs make it easier for workers to install rivet nuts with less effort. Lever-action tools now feature longer handles, reducing the amount of force required to compress the rivet nut, making manual installation quicker and more comfortable.
Some tools are also equipped with adjustable settings, allowing users to tailor the tool to fit different rivet nut sizes without needing separate tools for each size. These developments improve the usability of manual rivet nut tools, especially in applications that do not require automated solutions.
2. Power-Operated Rivet Nut Tools
One of the most significant innovations in rivet nut installation tools is the introduction of power-operated models. These tools are either pneumatic or battery-powered and are designed to automate the rivet nut installation process, which greatly reduces the time required to install each nut.
- Pneumatic Tools: Powered by compressed air, pneumatic rivet nut installation tools offer high-speed and consistent installation. They are ideal for heavy-duty applications where a large number of rivet nuts need to be installed quickly. These tools also offer adjustable pressure settings, ensuring that each rivet nut is installed with the correct torque for a reliable and durable fastening.
- Battery-Powered Tools: With advancements in battery technology, portable and efficient rivet nut installation tools have become more accessible. Battery-powered tools provide the mobility and flexibility that pneumatic tools may lack, allowing workers to install rivet nuts in hard-to-reach areas without being tethered to an air compressor. Many of these tools come with high-capacity lithium-ion batteries, which provide long operating times and quick charging.
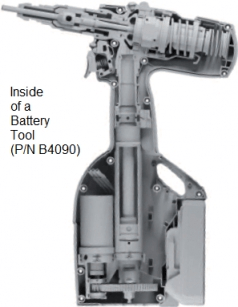
3. Smart Installation Tools with Digital Controls
Digital technology has made its way into rivet nut installation tools, bringing with it increased precision and control. Some advanced tools now feature digital torque controls, allowing for highly accurate installation of rivet nuts, particularly in applications where uniformity is crucial. These tools can automatically adjust to the material’s thickness and ensure consistent performance across a range of applications.
Additionally, smart tools may include data tracking capabilities, allowing operators to monitor the installation process and ensure each rivet nut is installed to the correct specifications. This level of control is particularly important in industries such as aerospace and automotive manufacturing, where the integrity of fastenings is critical.
4. Quick-Change Mandrels and Nosepieces
One of the most time-consuming aspects of rivet nut installation has traditionally been changing the mandrel or nosepiece when switching between different rivet nut sizes. Innovations in quick-change systems have streamlined this process, allowing operators to switch mandrels in seconds without the need for additional tools. This not only increases productivity but also reduces downtime, making it easier to handle a variety of rivet nut sizes in a single operation.
Some tools even feature automatic mandrel resetting, which returns the mandrel to the starting position after each installation, further speeding up the process and ensuring the tool is ready for the next rivet nut.
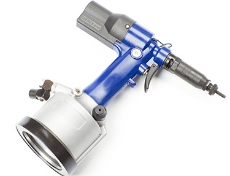
5. Cordless and Lightweight Designs
Portability and ease of use are key considerations for rivet nut installation tools. Recent innovations focus on creating cordless, lightweight tools that offer the same power and performance as their heavier, corded counterparts. This shift allows for greater flexibility, especially in applications where access to power sources is limited or when working in confined spaces.
These lightweight designs reduce operator fatigue during extended use and provide greater maneuverability, which is particularly beneficial in industries like construction and automotive repair, where fasteners often need to be installed in difficult-to-reach areas.
6. Integrated Safety Features
Safety is a crucial factor in any industrial tool design, and advanced rivet nut installation tools come equipped with a range of safety features. For example, some tools include automatic shut-off mechanisms that prevent over-tightening, which could damage the workpiece or cause injury to the operator. Additionally, improved grip and slip-resistant surfaces reduce the risk of accidents during installation.
Many pneumatic and battery-powered tools also include noise reduction technology, minimizing the sound produced during installation and contributing to a safer and more comfortable working environment.
7. Customizable and Industry-Specific Tools
Manufacturers are now offering rivet nut installation tools that can be customized to meet the specific needs of different industries. For instance, tools designed for automotive manufacturing may include features for faster cycle times, while those for aerospace applications may focus on higher precision and torque control. Customization allows these tools to meet the unique demands of each industry, ensuring optimal performance and reliability.
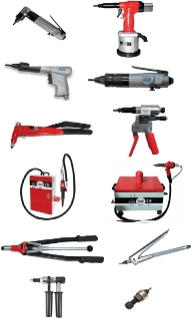
To sum up, innovations in rivet nut installation tools have transformed the way industries approach fastening. These advancements have made rivet nut installation faster, more precise, and easier for operators.