In mechanical assembly and structural fastening, lock washers and lock nuts are two common anti-loosening tools. They effectively prevent bolts and nuts from loosening due to vibrations or pressure changes. Although their functions are similar, these two tools have distinct differences. Read this article to gain a deeper understanding of lock washers vs lock nuts.
Part 1. What is Lock Washer?
Lock washer is a fastening component used to prevent nuts or bolts from loosening due to vibration or pressure changes. It is typically placed between the nut and the surface being fastened and works by providing additional friction to tighten the connection. The design of lock washers often involves compressing, elastic deformation, or wave-like shapes to increase the contact force between surfaces, preventing the nut from loosening.
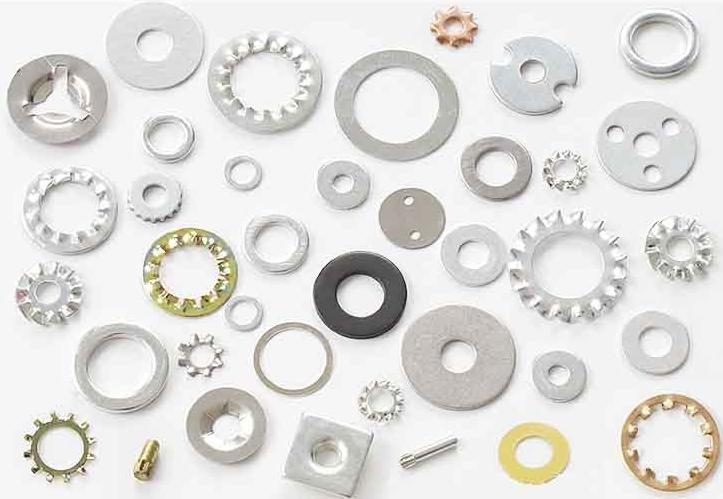
1. Types of Lock Washers
Spring Lock Washer: Spring lock washer is the most common type of lock washer, typically circular or wave-shaped, which uses elastic deformation to increase friction and prevent loosening.
Wave Lock Washer: Wave lock washers have a wavy shape and have strong elasticity and compression ability, making them suitable for environments with high vibration.
Tooth Lock Washer: Tooth lock washer has toothed edges that dig into the surface when installed, increasing friction and preventing loosening.
Serrated Lock Washer: Serrated lock washers have serrated edges that tightly grip the nut or bolt, improving the anti-loosening effect.
Double Lock Washer: This type of washer is composed of two nested washers, providing enhanced anti-loosening performance, ideal for high-load or extreme working conditions.
2. Pros & Cons of Lock Washers
Pros:
- Easy to install and cost-effective.
- Widely applicable in various mechanical and small assembly environments.
- Very convenient for situations that require frequent disassembly or adjustment.
- Provides additional friction to effectively prevent loosening.
Cons:
- Limited anti-loosening effect in high-load or high-vibration environments.
- Requires regular inspection and may need replacement.
- May require specific matching with bolts or nuts.
3. Use Cases of Lock Washers
Lock washers are typically used in low to medium-load scenarios, such as:
- Household appliances, automotive parts, and machine equipment fastening.
- Electronics, furniture, and other products where vibration is minimal.
- Mechanical equipment that requires frequent disassembly or adjustment.
Part 2. What is Lock Nut?
Lock nut is a type of nut that features a specially designed internal or external structure, used to prevent loosening of bolts or threaded connections due to vibration or external forces. Unlike standard nuts, lock nuts typically have a nylon insert or metal deformation structure that provides stronger anti-loosening properties.
1. Types of Lock Ncuts
Nylon Insert Lock Nut: The nylon lock nut has a nylon insert inside. The nylon insert tightly contacts the bolt or threads when installed, providing additional friction to effectively prevent loosening.
All-Metal Lock Nut: This type of lock nut uses metal material and uses specially designed metal deformation to provide anti-loosening. It is suitable for both high-temperature and high-load environments.
Spring Lock Nut: Spring lock nuts use the properties of springs to enhance fastening, making them suitable for environments with significant vibration.
Double Lock Nut: A double lock nut consists of two nested lock nuts, providing extra anti-loosening performance and used in situations requiring higher safety.
2. Pros & Cons of Lock Nut
Pros:
- Provides strong anti-loosening capability, ideal for high-load and high-vibration environments.
- No additional components are required during installation, saving time and cost.
- Performs well in high-temperature, high-pressure, and other specialized environments.
- Longer lifespan with lower maintenance requirements.
Cons:
- Requires torque control during installation to avoid damaging threads or the locking structure.
- Relatively higher cost compared to regular nuts.
- Not suitable for situations that require frequent disassembly and adjustment.
3. Use Cases of Lock Nuts
Lock nuts are widely used in industries that require high-strength anti-loosening protection, including:
- Automotive Industry: Fastening components in vehicles, engines, and other high-vibration parts.
- Machinery Manufacturing: Used in heavy machinery and industrial equipment for fastening purposes.
- Aerospace: Fastening parts in aircraft, rockets, and other high-load, high-safety applications.
- Construction: Used for securing connections in heavy structures to ensure long-term stability.
Part 3. Difference Between Lock Washer vs Lock Nut
While lock washers and lock nuts serve similar purposes, they have distinct characteristics and applications. Here’s a summary of the key differences between the two.
1. Design and Structure
Lock Washer: Lock washer is a flat washer with a specific design, such as a toothed, split, or serrated edge, which grips the surfaces of the fastened parts (like the bolt or nut).
This design helps create friction to resist loosening. Some common types include split lock washers, external tooth washers, and internal tooth washers.
Lock Nut: Lock nut is a type of nut that features an internal mechanism or additional locking feature to prevent it from loosening.
This might include a nylon insert (nylon lock nut), a deformed shape (prevailing torque lock nut), or a special thread design to resist loosening under vibration.
2. Application
Lock Washer: Typically used with standard nuts and bolts, lock washers are placed between the nut and the surface being fastened. The washer’s design helps maintain tightness by increasing friction.
Lock Nut: Lock nuts are used as a substitute for a regular nut and do not require a separate washer. They provide a locking mechanism directly within the nut itself, offering a more streamlined fastening solution.
3. Ease of Use
Lock Washer: Requires an additional step in the assembly process, as it must be placed under the nut or bolt head. This adds a layer of complexity but allows for more flexibility with different types of fasteners.
Lock Nut: Easier to use as it can be directly screwed onto the bolt or threaded rod, eliminating the need for a separate washer. Lock nuts offer a more straightforward approach to preventing loosening.
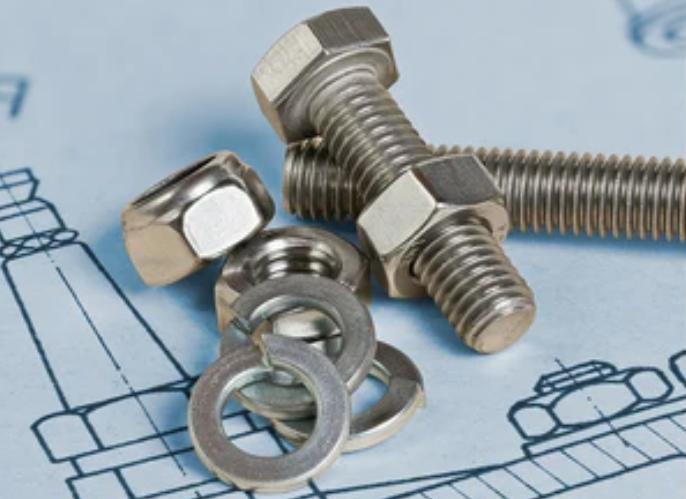
4. Effectiveness
Lock Washer: Generally effective in applications where vibrations or pressure fluctuations are moderate. However, over time, lock washers can lose their effectiveness due to wear or deformation.
Lock Nut: Typically provides a stronger and more durable locking action, especially when dealing with higher vibrations or extreme pressure. The design of lock nuts, such as the nylon insert or deformed threads, offers a more reliable and long-lasting solution.
5. Cost
Lock Washer: Lock washers are usually cheaper than lock nuts as they are simpler in design and manufacturing.
Lock Nut: Lock nuts tend to be more expensive than lock washers due to their more complex design and materials (e.g., nylon or specialized coatings).
Part 4. How to Choose the Right Locking Components?
When choosing between a lock washer and a lock nut, you can consider the following factors that may help you make the decisionn:
Load Requirements: For applications that need to withstand heavy loads, it is recommended to use a lock nut to ensure the stability of the connection.
Vibration Impact: In high-vibration environments, a lock nut typically provides better anti-loosening performance.
Installation Space: Lock washers are usually thinner and take up less space. If space is limited, a lock washer may be the better choice.
Cost Consideration: Lock washers are generally less expensive than lock nuts, so if cost is a key factor, a lock washer may be the more cost-effective option.
KENENG: High Quality Fasteners Manufacturer
When choosing the right locking components, it’s important to understand the characteristics and advantages of each type of part. As a leading manufacturer of fasteners, KENENG is dedicated to providing high-quality custom fasteners services to our customers. If you’re looking for a reliable parts processing manufacturer, KENENG is the partner you can trust.