Washers are crucial components in many mechanical assemblies. They are typically placed beneath a screw or bolt head to distribute load, prevent damage to the surface, or provide additional sealing. Custom washers are seemingly simple components can significantly impact the success of a engineering project, particularly in specialized applications that demand unique solutions.
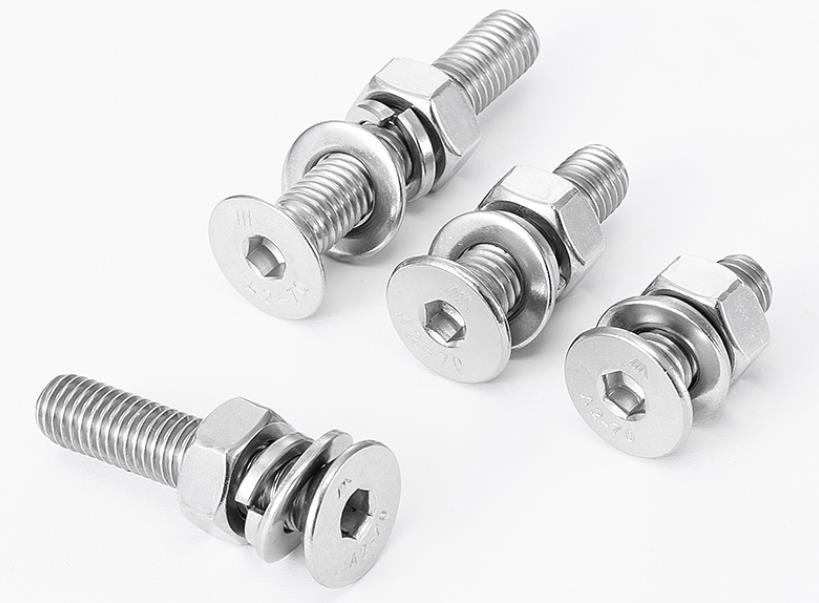
Why Need Custom Washers
While standard washers are readily available, they may not always meet the specific requirements of a particular application. Custom washers, on the other hand, can be tailored to address unique needs, such as:
- Non-standard dimensions: Unique inner and outer diameters, thicknesses, and bevels.
- Specialized materials: High-strength alloys, corrosion-resistant metals, or exotic materials like beryllium copper or Inconel.
- Complex geometries: Special shapes, serrations, or perforations for specific functions.
- Specialized finishes: Coatings or treatments for corrosion resistance, lubricity, or electrical conductivity.
Key Benefits of Custom Washers
Custom washers offer several advantages that can significantly improve the performance and reliability of engineering applications.
1. Enhanced Performance
- Load Distribution: Custom washers can be designed to distribute load more evenly, reducing stress concentrations and preventing premature failure.
- Vibration Dampening: Specialized materials and geometries can absorb vibrations, minimizing wear and tear on components.
- Sealing: Custom washers can provide superior sealing capabilities, preventing leaks and contamination.
- Electrical Conductivity: Conductive materials and designs can ensure reliable electrical connections.
2. Improved Reliability
- Corrosion Resistance: Custom washers made from corrosion-resistant materials can withstand harsh environments, extending the life of equipment.
- Wear Resistance: Specialized coatings and materials can reduce wear, improving the durability of components.
- Fatigue Resistance: Optimized designs can mitigate fatigue failures, ensuring long-term reliability.
3. Cost-Effective Solutions
- Reduced Maintenance Costs: Custom washers can reduce maintenance requirements by improving component life and reliability.
- Optimized Designs: Tailored solutions can minimize material usage and manufacturing costs.
- Preventative Measures: By addressing specific challenges upfront, custom washers can avoid costly repairs and downtime.
Specialized Applications Demanding Custom Washers
1. Aerospace Industry
- High-Temperature and High-Pressure Applications: Aircraft engines and other components operate in extreme conditions, requiring washers made from high-temperature alloys like Inconel or Hastelloy.
- Lightweight and High-Strength Materials: To reduce aircraft weight, custom washers made from lightweight, high-strength materials like titanium or aluminum alloys are often used.
- Vibration-Dampening Solutions: To mitigate vibrations that can affect the performance and lifespan of sensitive equipment, custom washers with specific geometries and materials can be employed.
2. Automotive Industry
- Corrosion-Resistant Washers: Vehicles are exposed to various harsh environmental conditions, including road salt, moisture, and chemicals. Custom washers made from stainless steel or other corrosion-resistant materials are essential to prevent rust and premature failure.
- Heat-Dissipating Washers: In high-temperature areas like engine compartments, custom washers with specialized thermal conductivity properties can help dissipate heat and prevent overheating.
- Vibration-Isolating Washers: To reduce noise, vibration, and harshness, custom washers with specific damping properties can be used in suspension systems and other critical components.
3. Electronics Industry
- Conductive Washers: In electronic assemblies, conductive washers made from materials like beryllium copper or phosphor bronze are used to ensure reliable electrical connections.
- Non-Conductive Washers: To prevent short circuits and electrical leakage, non-conductive washers made from materials like nylon or Teflon are employed.
- Heat-Sink Washers: To dissipate heat from electronic components, custom washers with high thermal conductivity can be used to improve performance and reliability.
4. Medical Device Industry
- Biocompatible Materials: Medical devices that come into contact with the human body must be made from biocompatible materials. Custom washers made from materials like titanium or stainless steel can be used in implants and other medical devices.
- Precision-Engineered Washers: Medical devices often require high precision and accuracy. Custom washers with tight tolerances can ensure the proper functioning of these devices.
- Sterilizable and Corrosion-Resistant Washers: Medical devices must be sterilized to prevent infection. Custom washers made from materials that can withstand sterilization processes and resist corrosion are essential.
5. Oil and Gas Industry
- High-Pressure and High-Temperature Applications: Oil and gas equipment operates in harsh environments with extreme pressures and temperatures. Custom washers made from high-strength, corrosion-resistant materials like Inconel or Hastelloy can withstand these conditions.
- Corrosion-Resistant Materials: To prevent corrosion caused by exposure to corrosive substances like saltwater and hydrocarbons, custom washers made from materials like stainless steel or nickel alloys are used.
- Vibration-Dampening Washers: To reduce vibrations in critical equipment, custom washers with specific damping properties can be employed.
6. Renewable Energy Industry
- Corrosion-Resistant Washers: In marine and offshore applications, custom washers made from corrosion-resistant materials like stainless steel or nickel alloys are essential to prevent damage from saltwater and other corrosive substances.
- Vibration-Isolating Washers: To reduce vibrations in wind turbines and other renewable energy equipment, custom washers with specific damping properties can be used.
- High-Strength Washers: For solar panel installations and other structural applications, custom washers made from high-strength materials can ensure the integrity of the structure.
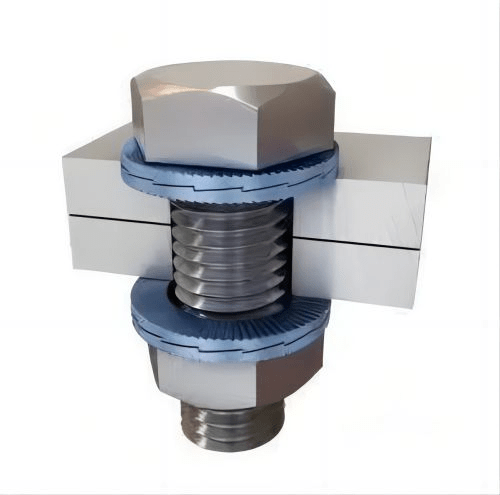
Design Considerations for Custom Washers
This sheet provides a comprehensive overview of the various design considerations that should be taken into account when creating custom washers. It ensures that the washers are not only functional but also meet specific performance and environmental standards.
Design Considerations | Description |
Material Selection | Choose materials based on specific application scenarios and requirements. Common materials include carbon structural steel (e.g., Q235), stainless steel, aluminum alloy, etc., which need to possess good punchability, sufficient strength, and good surface quality. |
Load and Deflection Performance | The key characteristics of a spring washer are how much it will deflect under a given load and at what point it will flatten. These values are typically represented in Load/Deflection (L/D) curves. |
Environmental Concerns | Consider the operating environment’s impact on the washer’s load-bearing and reactive characteristics. Temperature and exposure to corrosive agents are critical factors, and material specifications must account for these environmental conditions. |
Match Washer and Bolt Strength | Select washer types that properly pair with bolt strength to avoid deformation under high stress. For example, a grade 8 bolt with 150,000 psi tensile strength requires a hardened washer with 100,000 psi+ to maintain joint integrity and load distribution. |
Sustainability and Environmental Regulations | Opt for washers made using sustainable manufacturing processes to reduce carbon impact on the environment. Consider environmental regulations like RoHS (Restriction of Hazardous Substances) to minimize environmental hazards. |
Type of Material | Different materials offer different benefits:Stainless steel washers provide strength and corrosion resistance, suitable for marine conditions.Nylon washers are lightweight, offer electrical insulation, and are appropriate for electronics.Brass washers resist dezincification and are preferred for plumbing operations. |
Tolerances | Thickness Tolerance: ±0.1mm for sizes up to M20.Inside Diameter Tolerance: +0.3mm to +0.5mm. |
Hardness | Typically between 140-200 HV. |
Finish | Options include phosphate or zinc-plated finishes. |
Internal Diameter | Ranges from 3mm to 72mm. |
Spring Compensation or Deflection | There is an inverse relationship between washer thickness and spring compensation or deflection. The physical design of washers can be varied to serve either or both of these basic performance characteristics. |
Space Envelope | Wave washers and conical washers increase only slightly in diameter as they are compressed. Consider the overall space occupied by a spring washer, described as a hollow “cylinder,” when specifying spring washers. |
Unique Shapes and Designs | Custom washers can be designed for non-standard requirements, including irregular shapes and unconventional configurations, to suit specific application needs. |
Surface Treatments | Options for coatings and finishes, such as corrosion resistance, electrical insulation, or wear resistance, add functionality and durability to the washers. |

Manufacturing Techniques for Custom Washers
The manufacturing technique employed for a custom washer depends on factors such as the required quantity, complexity of the geometry, material, and desired tolerances.
1. Stamping
- Best for: High-volume production of simple shapes and sizes.
- Process: Metal sheets are fed into a stamping press, where a punch and die cut out the washer shape.
- Advantages: High production rates, low cost per unit.
- Limitations: Limited to simple shapes and may not be suitable for complex geometries or high-precision tolerances.
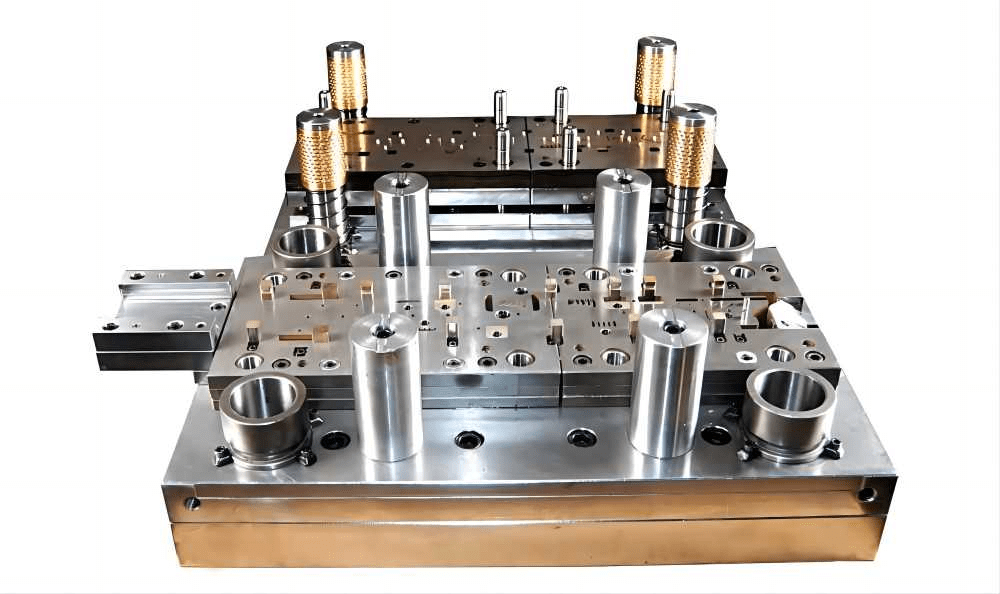
2. Machining
- Best for: Low-volume production of complex shapes and high-precision tolerances.
- Process: A cutting tool removes material from a solid block of metal to form the desired washer shape.
- Advantages: High precision, versatility for complex shapes.
- Limitations: Lower production rates, higher cost per unit compared to stamping.
3. Additive Manufacturing (3D Printing)
- Best for: Prototyping, low-volume production of complex geometries, and specialized materials.
- Process: Material is added layer by layer to create the 3D shape of the washer.
- Advantages: Design flexibility, ability to produce complex shapes, and potential for rapid prototyping.
- Limitations: Lower production rates, higher cost per unit, and limitations in material choices.
4. Forging
- Best for: High-volume production of complex shapes and high-strength parts.
- Process: Metal is shaped by hammering or pressing it into a die.
- Advantages: High strength, good dimensional accuracy, and potential for high production rates.
- Limitations: High initial tooling costs, limited design flexibility.
5. Powder Metallurgy
Best for: Producing complex shapes with precise control over porosity and material properties.
Process: Metal powder is compacted into a desired shape and then sintered to bond the particles together.
Advantages: High strength, good wear resistance, and ability to produce complex shapes.
Limitations: Higher cost compared to other methods, limited material choices.
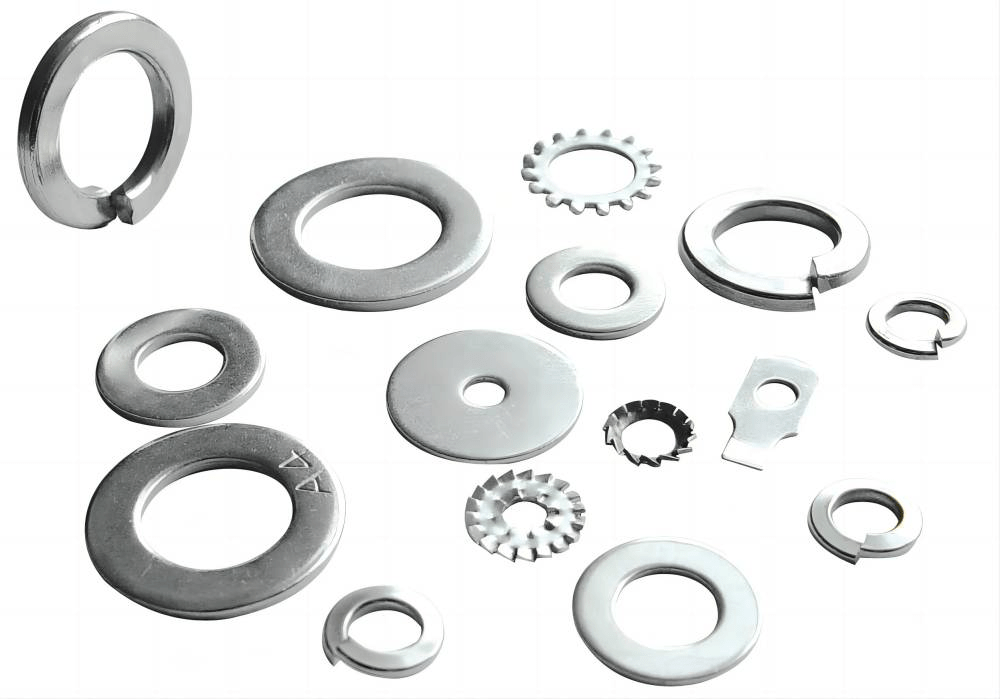
Quality Control and Testing for Custom Washers
This chart provides a comprehensive overview of the quality control and testing measures that should be implemented for custom washers to ensure they meet the highest standards of quality and performance.
Quality Control and Testing Steps | Description |
Material Inspection | Verify the material’s composition, heat treatment, and quality upon receipt. Conduct metallurgical analysis to ensure the material properties meet the standards. |
Process Control | Implement strict process control measures for heat treatment, machining, threading, and any other manufacturing steps. Maintain consistent process parameters to ensure uniform quality. |
Inspection Points | Introduce inspection points at various stages of manufacturing to check for defects, dimensions, and quality. Inspect threading, dimensions, surface finish, and other critical parameters. |
Sampling and Testing | Regularly sample products for testing, such as tensile testing, hardness testing, and metallurgical analysis, to ensure they meet the required specifications. |
Thread Inspection | Thoroughly inspect threading using proper thread gauges to ensure accurate dimensions and fit with mating components. |
Traceability | Implement a traceability system to track each fastener’s journey from raw material to final product. This aids in accountability and recalls if necessary. |
Dimensional Inspection | Precise measurement to ensure exact dimensions of the washers. |
Surface Finish Evaluation | Assessment of the washer’s finish and coating. |
Material Testing | Verification of material properties and durability. |
Torque and Tension Testing | Assessment of load-bearing and fastening ability. |
Salt Spray Testing | Corrosion resistance evaluation under harsh conditions. |
Certification and Compliance | Compliance with industry standards and regulations. |
Riboflavin Coverage Testing | Performed on the process contact parts being used in the washer to ensure validatable coverage. |
Cabinet Washer Chamber Design and Testing | Should be the same as BPE vessel construction standards. |
Interface with Surrounding Installation Area | Consideration of the exterior interface of the cabinet washer with the surrounding installation area, including surface finish requirements, door interlocking, and safety features. |
Turnover Package Documentation | Documentation requirements of the cabinet washer shall meet existing BPE requirements. |
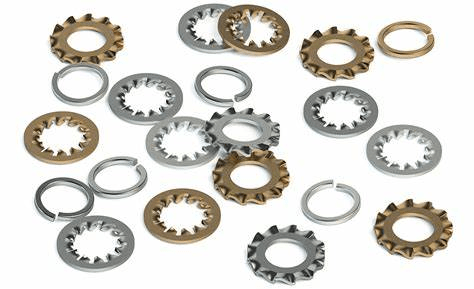
In summary, through understanding the unique requirements of custom washers, leveraging advanced manufacturing techniques and taking strict quality control and testing measures, engineers can design and produce custom washers that optimize performance, improve reliability, and reduce costs.