Stainless steel screws are widely used in construction, industry, home repairs, and other fields due to their excellent corrosion resistance. They are often perceived as rust-proof, but in reality, we frequently hear complaints from people who experience rusting even with stainless steel screws. So, do stainless steel screws rust? Read this post, we will reveal everything about stainless steel!
Part 1. What is Stainless Steal Screw?
Stainless steel screws are fasteners made from stainless steel, known for their strong oxidation and corrosion resistance. Common materials include 304 and 316 stainless steel, which have different chemical compositions.
304 screws are suitable for general industrial use, while 316 screws with higher molybdenum content offer better corrosion resistance, especially in harsh environments like seawater.
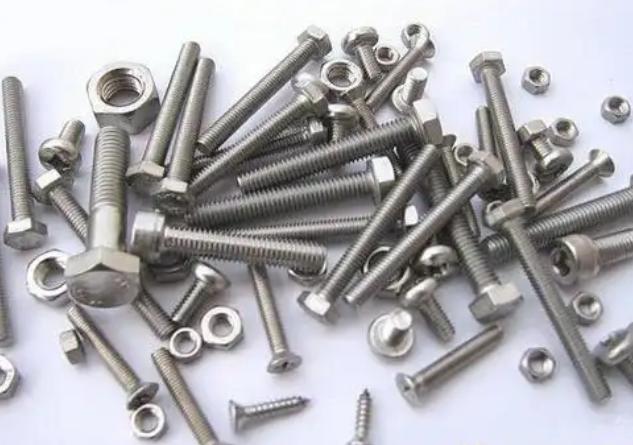
Key Features of Stainless Steel Screws
Strong corrosion resistance: Compared to regular steel, stainless steel has better resistance to corrosion and can withstand chemical attacks.
High temperature resistance: Stainless steel can withstand high temperatures without easily breaking down or corroding.
Smooth appearance: Stainless steel has a smooth surface, is less prone to rusting, and maintains a neat, clean appearance.
Corrosion Resistance Principle of Stainless Steel Screws
The main components of stainless steel screws are iron, chromium, and nickel. Specifically, chromium forms a thin protective layer of chromium oxide film on the surface of stainless steel.
This film has strong corrosion resistance and effectively prevents chemical reactions between water, oxygen in the air, and metal. However, this layer is not absolutely indestructible.
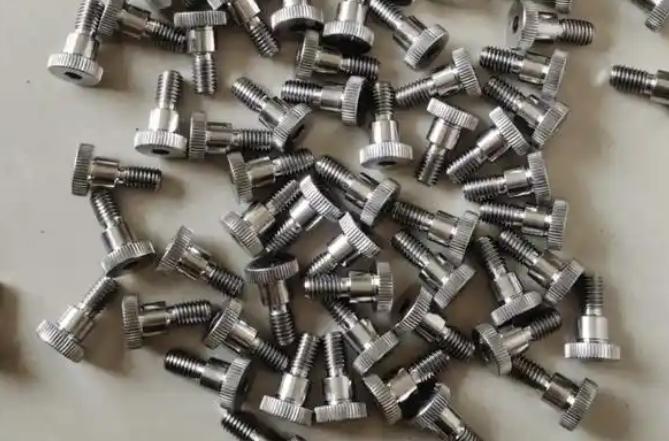
Part 2. Will Stainless Steel Screws Rust?
Although stainless steel screws have strong resistance to corrosion, they are not completely rust-proof. In certain special environments, stainless steel screws may still experience rusting. Let’s take a look at the reasons why stainless steel screws may rust.
Reasons of Stainless Steel Screws Rust
Environmental Factors
The corrosion resistance of stainless steel screws mainly depends on the oxide film formed on their surface, which prevents external substances from entering the metal.
However, if the screws are exposed to high humidity, salt mist, or other corrosive substances (such as acidic or alkaline environments) for a long time, the oxide film may be damaged, leading to metal corrosion.
This is especially true in harsh environments like coastal areas or chemical plants, where 304 stainless steel screws are prone to rusting.
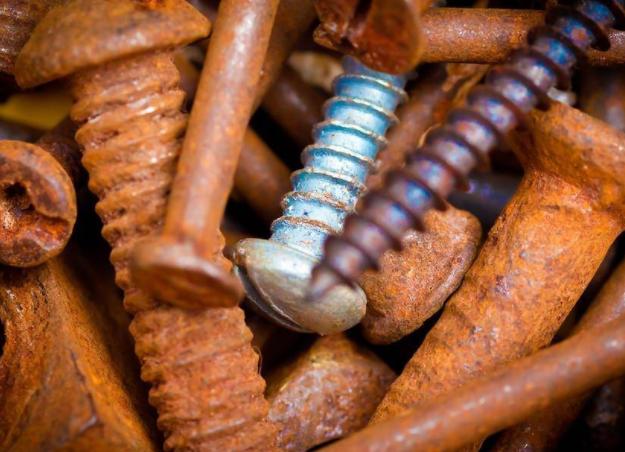
Stainless Steel Quality Issues
The corrosion resistance of stainless steel is closely related to its composition. 304 stainless steel contains 18% chromium and 8% nickel, which provides good corrosion resistance but can still be vulnerable in some harsh environments.
316 stainless steel, which contains a higher proportion of molybdenum, offers stronger corrosion resistance and is better suited for extreme environments like seawater.
Surface Damage
The oxide film on the surface of stainless steel screws can be mechanically damaged or scratched during installation, exposing the metal surface. This makes it more susceptible to oxidation, eventually leading to rust.
Usage Time
Over time, even in general environments, stainless steel screws may be affected by external factors, causing the oxide film to gradually lose its effectiveness, which can lead to corrosion.
Part 3. How to Remove Stainless Steel Screw Rust?
Here are some methods you can try to remove rust from stainless steel screws.
Use a Rust Remover: Apply a commercial rust remover or a paste made from baking soda and water. Let it sit for a few minutes, then scrub it with a wire brush or toothbrush.
Vinegar or Lemon Juice: Soak the screw in white vinegar or lemon juice for 10-15 minutes. Acid helps dissolve rust. Scrub with a brush afterward.
Use a Stainless Steel Cleaner: After removing the rust, clean the screw with a stainless steel cleaner to restore its shine and prevent future rusting.
Polish: Once cleaned, polish the screw with a soft cloth to remove any remaining stains and protect it from further corrosion.
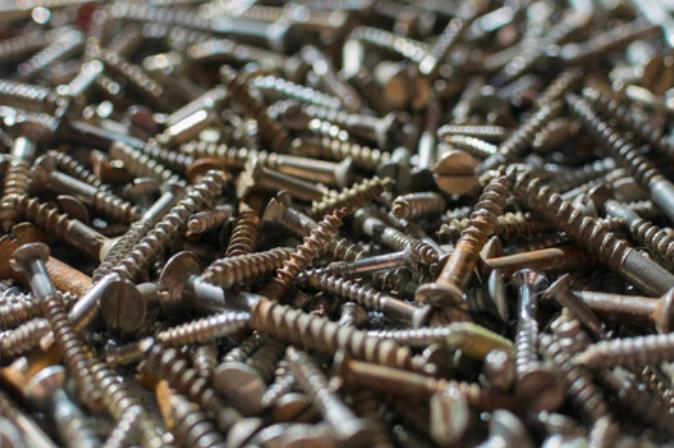
Part 4. How to Prevent Stainless Steel Screw Rust?
Although stainless steel screws have strong corrosion resistance, we can still take some measures to prevent screws from rusting.
Choose Right Material
When selecting stainless steel screws, choose the appropriate material based on the specific environment of use. For general indoor applications, 304 stainless steel screws are sufficient.
However, for use in coastal areas, chemical plants, or extremely humid environments, it is recommended to choose 316 stainless steel screws or specially treated high-corrosion-resistant stainless steel materials.
Also, some high-manganese, low-nickel alloy materials have been available on the market, labeled as 304 or 316 stainless steel.
However, these alloys have lower chromium content and may not be suitable for certain environments or applications, posing a potential quality risk. Therefore, when choosing stainless steel screws, make sure to select the genuine material and avoid potential issues.
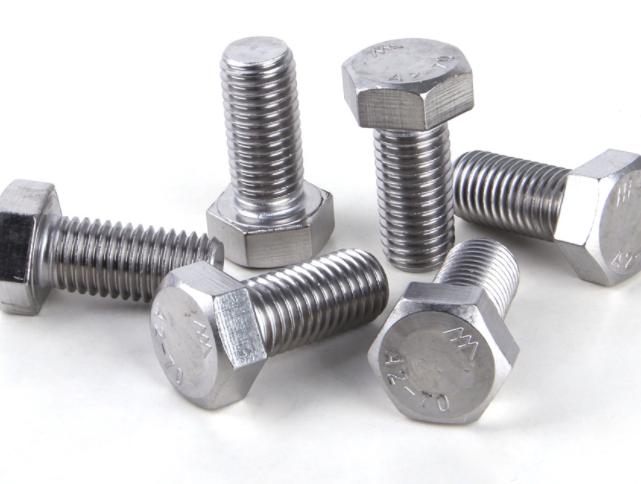
Avoid Mechanical Damage
When installing stainless steel screws, avoid applying excessive force that could scratch or damage the protective film on the screw’s surface. Screws that have damaged protective films should be replaced promptly to prevent compromising their corrosion resistance.
Regular Maintenance
Regularly check the condition of stainless steel screws and clean off any accumulated contaminants, especially in humid, acidic, or chloride-containing environments. It is crucial to promptly remove salts, oil, and chemicals from the surface to maintain the integrity of stainless steel.
Coating Protection
For screws that will be exposed to harsh environments for extended periods, consider using anti-corrosion coatings or electroplating (such as zinc plating, nickel plating, etc.). These external coatings can further enhance the screw’s corrosion resistance, especially in highly corrosive environments.
Final Thoughts
Generally, stainless steel screws are considered to be rust-resistant due to their excellent resistance to corrosion. However, under certain specific conditions, such as being exposed to saltwater, acidic or alkaline substances, stainless steel screws can still rust.
To sustain the long-term use of stainless steel screws, it’s crucial to select the appropriate material, properly install them, and regularly maintain them. KENENG offers high-quality, reliable stainless steel screws that are durable and perform well even in challenging environments.
FAQs
What screws do not rust?
Screws that are made from materials with high resistance to corrosion, such as stainless steel, brass, bronze, and titanium, are less likely to rust. Among these, 316 stainless steel screws are particularly resistant to rust and corrosion, especially in harsh environments like marine or chemical settings, due to the addition of molybdenum.
Brass and bronze screws, made of copper, have strong corrosion resistance, especially in freshwater environments. Titanium screws are highly resistant to rust and corrosion, even in extreme conditions like seawater, making them an excellent choice for demanding applications.
What are the disadvantages of stainless steel screws?
Stainless steel screws are more expensive than regular steel screws and can be prone to galling (seizing) during installation, requiring lubricants or special tools. They also have lower tensile strength compared to carbon steel, making them unsuitable for heavy-duty applications. While resistant to rust, they can still suffer from pitting or crevice corrosion in harsh environments if the protective oxide layer is damaged.
How long will stainless steel screws last?
Stainless steel screws can last for many years, even decades, in mild conditions. In harsh environments, such as coastal areas or chemical settings, their lifespan may be shorter due to corrosion. High-quality stainless steel, such as 316, lasts longer and proper maintenance can enhance its durability.
How to tell if a screw is stainless steel?
To tell if a screw is stainless steel, use a magnet test—stainless steel is usually non-magnetic, though some grades may be slightly magnetic. Stainless steel screws also resist rust, so they won’t show signs of corrosion. You can also check for markings like “SS” or specific grades (e.g., 304, 316).