Precision metal stamping plays a vital role in manufacturing, creating essential components for industries like automotive, electronics, aerospace, and medical devices. By using high-tonnage presses and carefully crafted metal stamping dies, manufacturers can produce intricate and highly accurate metal parts at scale. Understanding the processes, differences between methods, tooling’s role, and strategies for improving quality and consistency is essential for anyone involved in or considering precision metal stamping.
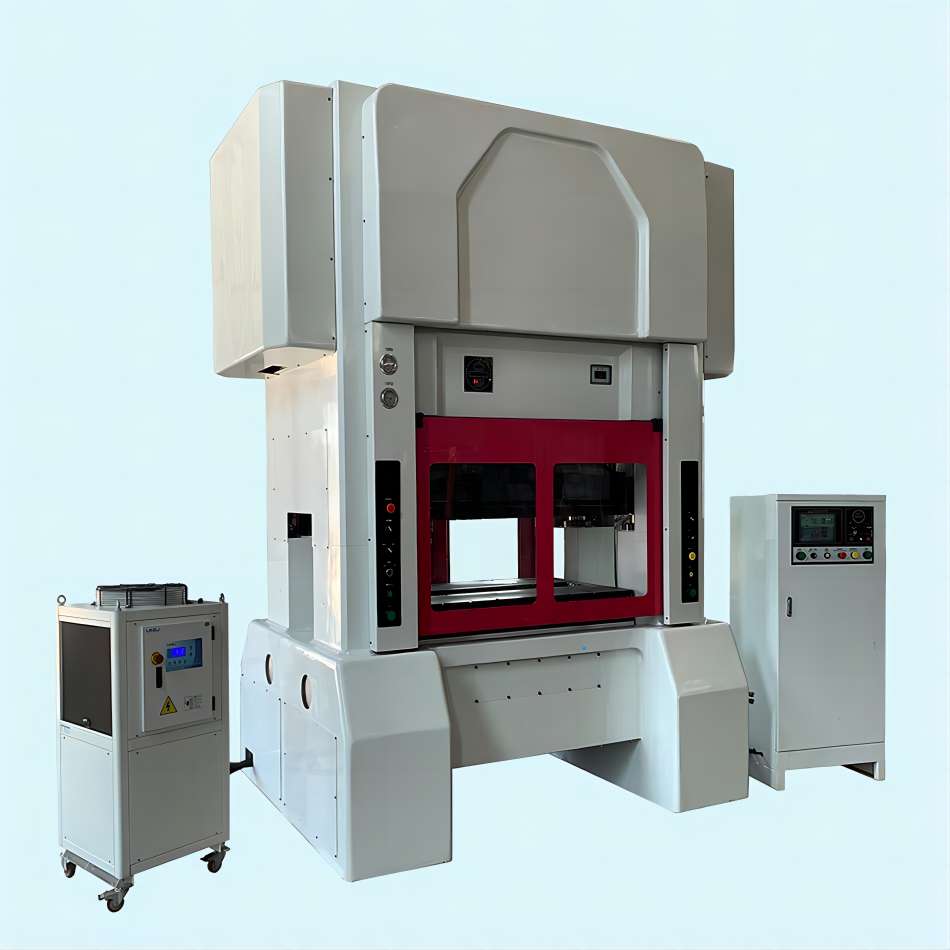
What are the Different Types of Precision Metal Stamping Processes?
Precision metal stamping uses various methods, each tailored to specific part designs and industry requirements. The types of stamping processes often vary in terms of complexity, application, and material used, but they all share a common goal: to produce high-precision parts quickly and efficiently. Here are some of the primary types of precision metal stamping processes used in modern manufacturing:
Precision Metal Stamping Process | Description | Applications |
Blanking | Removes a specific piece of metal from a larger sheet to serve as raw material for further stamping. Efficient for producing uniform pieces with minimal waste. | Ideal for applications requiring consistent shapes, commonly used as a preliminary step in many stamping operations. |
Embossing | Creates raised or recessed designs on the metal surface, adding details like logos or part numbers without affecting structural integrity. | Commonly used in automotive and appliance industries for aesthetic appeal and branding. |
Bending | Forms metal into specific angles or shapes with controlled curves, essential for parts that need precise fits. | Frequently used for brackets, clips, and mounting components across various industries. |
Coining | Applies high pressure to create detailed designs and patterns on metal, achieving tight tolerances. | Often used in electronics manufacturing for high-precision components. |
Piercing and Notching | Creates holes or cutouts in metal sheets, allowing for attachment points, ventilation, or specific shapes with high accuracy. | Suitable for designs requiring complex shapes and exact specifications, common in electronics and automotive applications. |
Each of these processes has distinct advantages and is suited for specific applications. Choosing the right metal stamping process is crucial for achieving the desired balance between quality, efficiency, and cost.
How is Progressive Die Stamping Different from Transfer Die Stamping?
Two of the most popular methods in precision metal stamping are progressive die stamping and transfer die stamping. Each offers unique advantages and is best suited to specific types of parts and production volumes. Understanding the differences between these methods is essential for selecting the right process for a given project.
Stamping Method | Process Description | Advantages | Best Suited For |
Progressive Die Stamping | A metal strip moves through a series of stations, each performing a unique operation (blanking, piercing, bending) as it advances. The part is separated from the strip at the end of the process. | Highly efficient, ideal for high-volume production, automated, consistent quality across production runs | Small, complex parts requiring multiple forming steps |
Transfer Die Stamping | A single blank is transferred from one station to the next using transfer mechanisms, allowing each station to perform a different operation. | Greater flexibility for larger parts and design complexity, allows customization | Large, unique, or complex-shaped parts, like automotive components |
Progressive die stamping is efficient for high-volume production of smaller, intricate parts, while transfer die stamping offers flexibility and customization, making it ideal for larger, complex parts.
What is the Role of Tooling in Precision Metal Stamping?
Tooling is a critical component in precision metal stamping, as it directly impacts the quality, efficiency, and cost of the final product. Tooling involves the design and production of metal stamping dies, which are customized to perform specific operations. Proper tooling can mean the difference between a high-quality, cost-effective part and one that requires frequent rework or results in high scrap rates.
- Tooling Components: Metal stamping dies are typically made of hardened steel or carbide, and they consist of various parts, including die sets, punches, and other elements necessary for shaping the metal. The die set provides the overall structure, while punches and dies create the desired shapes and designs. Material selection for tooling is crucial, as it impacts the durability and lifespan of the dies.
- Importance of Precision in Tooling: Precision in tooling ensures that each part meets exact specifications. Tolerances are essential in industries like aerospace and medical devices, where even minor deviations can impact performance and safety. Proper maintenance and regular calibration of tooling help maintain accuracy over time, reducing the risk of costly errors.
- Tooling Costs and Lifecycle: While the initial cost of tooling can be high, investing in quality tooling can lead to long-term savings. High-quality tooling lasts longer, requires less frequent replacement, and reduces the risk of downtime. Manufacturers must consider both the upfront cost and the potential lifecycle of tooling when planning a project.
How Can I Improve the Quality and Consistency of Precision Metal Stamping Parts?
In precision metal stamping, quality and consistency are crucial for product performance, appearance, and overall success. Achieving these objectives relies on quality control practices, understanding factors that affect consistency, and committing to continuous improvement.
- Quality Control Techniques: Metal stamping quality control combines visual inspection, dimensional checks, and automated inspection systems. Automated systems with sensors and cameras can quickly detect defects, ensuring each part meets strict tolerances. Visual inspections are also essential, particularly for parts where appearance is a priority. Dimensional checks are critical in high-precision industries, such as electronics and aerospace, to ensure parts meet exact specifications and avoid issues in assembly.
- Factors Affecting Consistency: Consistency in metal stamping is influenced by material properties, press accuracy, and environmental conditions. Metals vary in hardness, ductility, and wear resistance, all of which impact final product quality. Temperature and humidity can also affect the stamping process, especially for high-precision applications. Regular equipment calibration and reliable material sourcing are essential to minimize variability across production runs.
- Continuous Improvement Strategies: Continuous improvement is vital for sustaining quality and consistency in metal stamping. Feedback loops, informed by data from previous production runs, guide process optimization. Routine tooling maintenance, operator training, and regular equipment evaluations contribute to ongoing improvements and help prevent errors before they occur.
- New Technologies in Stamping: Emerging technologies, such as automation, data analytics, and real-time monitoring, are reshaping the metal stamping industry. Automated systems enhance both speed and accuracy, while data analytics identifies trends for better decision-making. Real-time monitoring detects issues in real time, reducing downtime and scrap rates and driving efficiency in quality control.
By integrating these strategies and technologies, manufacturers can achieve the high-quality, consistent output essential in precision metal stamping.
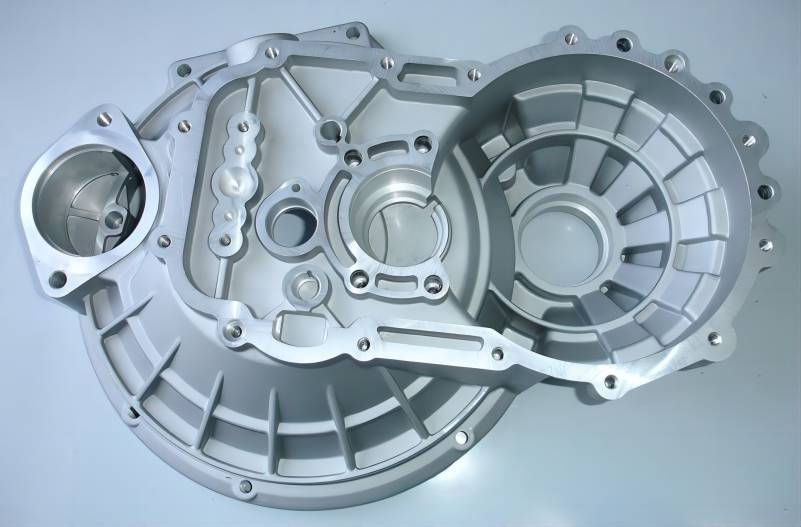
Precision metal stamping is a sophisticated field that requires a deep understanding of processes, tooling, and quality control. By mastering these core elements, manufacturers can produce high-quality, cost-effective parts that meet the demands of various industries. Whether it’s choosing the right stamping process, investing in quality tooling, or implementing continuous improvement strategies, each decision plays a role in the success of a precision metal stamping operation.