Tungsten steel milling cutters have become essential in machining applications, particularly where hard-to-machine materials are involved. The performance and efficiency of these tools are significantly influenced by their cutter geometries. Cutter geometries play a crucial role in enhancing cutting precision, minimizing tool wear, and improving the surface finish of tungsten steel milling cutters. This article explores the various cutter geometries in tungsten steel milling cutters, their importance in different machining applications, and how to choose the right cutter geometry.
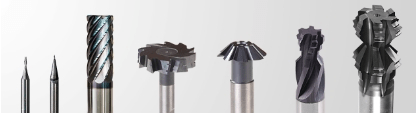
Various Cutter Geometries in Tungsten Steel Milling Cutters
1. Helix Angle
The helix angle is the angle at which the flute spirals around the cutter. It plays a pivotal role in determining how the tool interacts with the material:
- Standard Helix Angle (30° – 45°): This angle range balances cutting forces and chip evacuation, making it ideal for general-purpose machining.
- High Helix Angle (45° – 60°): With steeper angles, high-helix cutters enhance chip evacuation, making them suited for softer materials and high-speed cutting, as well as providing a better surface finish.
- Variable Helix Angle: Variable helix cutters have different angles on each flute, which disrupts harmonic vibration and reduces chatter, leading to smoother cuts and longer tool life, especially beneficial in high-speed and precision applications.
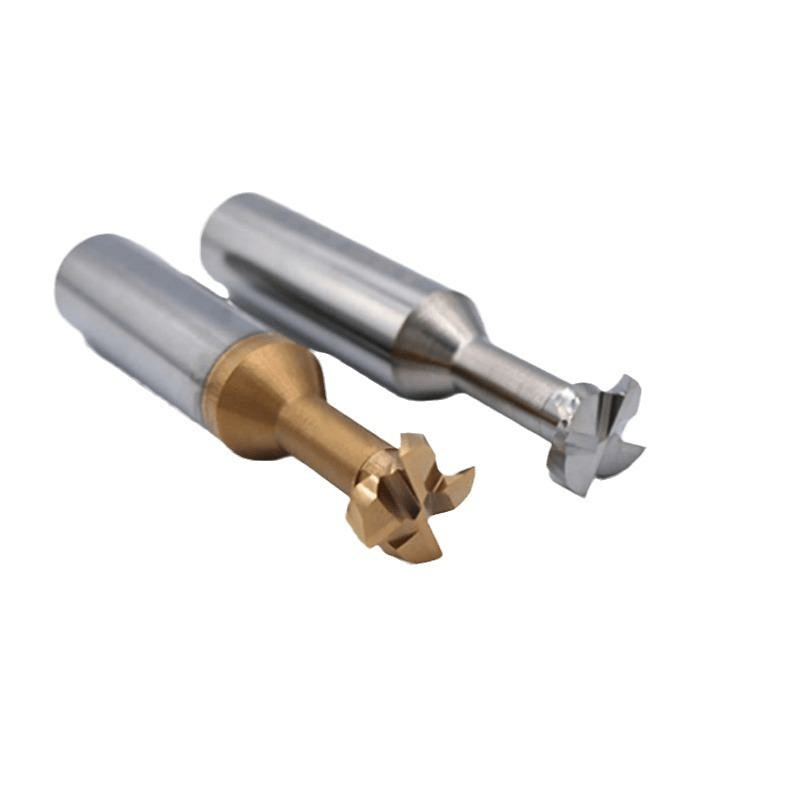
2. Flute Design
The flute design of tungsten steel milling cutters, including the number of flutes and flute geometry, impacts chip removal, cooling, and cutting efficiency.
- Two-Flute Cutters: Known for excellent chip evacuation and reduced friction, these are commonly used for soft materials and non-ferrous metals where chip buildup is less likely.
- Four-Flute Cutters: Providing a good balance of chip control and durability, four-flute designs are commonly used for harder materials, where finer finish and high feed rates are required.
- Variable Flute Spacing: Innovations in flute spacing, with uneven gaps between flutes, help to reduce vibration and increase stability during cutting. This is advantageous for high-speed machining and in applications that require a fine surface finish.
3. Corner Radius and Chamfer
The geometry at the corners of the cutter can significantly affect tool durability and the quality of the finished workpiece:
- Sharp Corners: These are commonly used for milling corners with precision but tend to wear quickly and may chip under heavy loads.
- Corner Radius: Adding a small radius at the corner reduces the stress concentration, enhancing the tool’s resistance to chipping. This is particularly useful in hard materials like steel or titanium, where sharp edges might wear faster.
- Chamfered Edges: Chamfered cutters are highly effective in applications requiring high feed rates, as they provide a reinforced cutting edge that can withstand the lateral forces encountered during aggressive cutting.
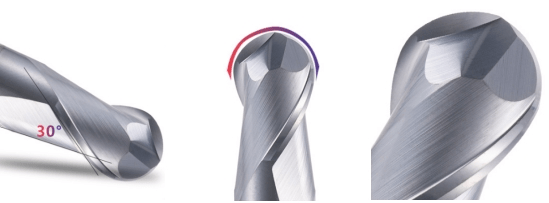
4. Cutting Edge Geometry
The geometry of the cutting edge itself, including the rake angle and clearance angle of tungsten steel milling cutters, determines how efficiently the cutter removes material.
- Positive Rake Angle: Positive rake cutters slice material more efficiently, reducing cutting forces and allowing for smoother cuts, which is ideal for softer materials and precise finishing.
- Negative Rake Angle: Negative rake tools are better suited for tougher materials, where a reinforced edge is necessary to withstand the higher cutting pressures. They offer durability at the expense of a slightly rougher finish.
- Multi-Faceted Cutting Edges: Multi-faceted edges reduce the cutting resistance by distributing force across multiple points. This is especially advantageous for minimizing tool deflection and improving durability.
5. Variable Pitch Design
A variable pitch design involves changing the spacing between each flute, which disrupts the harmonic frequencies that can cause vibration during cutting.
The benefits
- Reduced Vibration and Chatter: By minimizing the resonance that leads to vibration, variable pitch cutters enhance tool stability and enable smoother machining at higher speeds.
- Improved Surface Finish: With reduced chatter, the cutter can produce a more refined surface, which is crucial for applications requiring high surface quality.
- Longer Tool Life: The lack of vibration also reduces wear on the tool, allowing for a longer lifespan and fewer replacements.
6. Coatings that Complement Geometry
While not strictly part of the geometry, coatings play a vital role in enhancing the cutter’s performance. Various coatings are applied to tungsten steel cutters to improve heat resistance, reduce friction, and increase durability.
- TiAlN (Titanium Aluminum Nitride): This coating is highly resistant to heat and wear, making it suitable for high-speed applications and hard materials.
- DLC (Diamond-Like Carbon): DLC coatings reduce friction, improving performance on abrasive materials and extending tool life.
- AlCrN (Aluminum Chromium Nitride): Known for its high thermal resistance, this coating is ideal for machining heat-resistant alloys and materials.
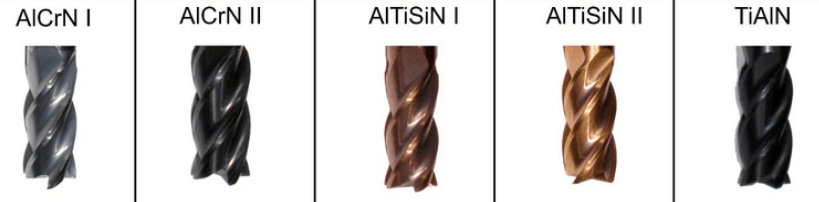
Selecting the Right Cutter Geometry for Tungsten Steel Milling Cutters in the Different Applications
Here’s a chart to help in selecting the appropriate cutter geometry based on machining goals and application conditions, optimizing performance, efficiency, and tool longevity of tungsten steel cutters.
Cutter Geometry | Ideal Applications | Benefits |
Helix Angle | – Low Helix: Roughing hard materials – Standard Helix: Versatile, general machining – High Helix: High-speed finishing on soft metals and plastics | – Low Helix: Durability, reduced chatter – Standard Helix: Balanced performance – High Helix: Smoother finish, faster chip evacuation |
Flute Design | – Two Flutes: Aluminum, soft metals – Four Flutes: Steel, titanium, hard alloys – Variable Flutes: High-speed precision applications | – Two Flutes: Better chip evacuation – Four Flutes: Better tool stability and feed rate – Variable Flutes: Reduced vibration, smoother finish |
Corner Radius / Chamfer | – Sharp Corners: Fine finishing, soft materials – Corner Radius: Hard metals, impact resistance – Chamfered: High feed-rate roughing | – Sharp Corners: Precision – Corner Radius: Reduces chipping in hard metals – Chamfered: Withstands high feed rates |
Cutting Edge Geometry | – Positive Rake: Soft materials, non-ferrous metals – Negative Rake: Hard metals like steel, titanium – Multi-Faceted: Precision work, thin materials | – Positive Rake: Lower cutting forces – Negative Rake: Better durability – Multi-Faceted: Smoother cuts, lower tool deflection |
Variable Pitch Design | – High-speed applications: Hard metals and precision applications | – Minimizes vibration, extends tool life, improves surface finish |
Coatings (Complementary) | – TiAlN: Hard metals, steel, titanium – DLC: Soft materials, aluminum – AlCrN: High-temperature applications | – Enhanced wear resistance, heat resistance, and optimized machining performance |
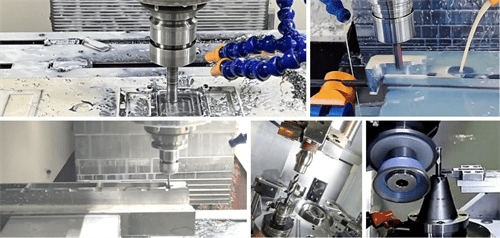
Innovations in Cutter Geometries for Tungsten Steel Milling Cutters
1. Optimized Helix Angles
The helix angle, or the angle at which the cutter’s flute spirals around the tool, plays a significant role in reducing cutting forces. Innovations in helix angle design have introduced variable helix angles, where each flute is set at a slightly different angle. This disrupts the natural vibration harmonics that occur during cutting, leading to:
- Reduced vibration and chatter: Variable helix angles minimize the resonance that causes vibration, allowing for smoother and more stable cuts.
- Improved surface finish: By dampening vibrations, these angles yield a finer surface finish, critical in applications like mold-making and precision machining.
- Longer tool life: Lowered cutting forces and reduced vibration help prevent tool wear, thus extending tool life.
2. Advanced Flute Designs
The flute geometry, particularly its depth, width, and shape, affects how efficiently chips are evacuated from the cutting area. Innovations in flute design have led to the development of larger, smoother flutes in tungsten steel milling cutters, resulting in:
- Enhanced chip evacuation: Wider flutes improve chip flow, especially when cutting dense materials, preventing re-cutting of chips and reducing tool wear.
- Better cooling efficiency: Larger flute spaces allow coolant to reach the cutting edge more effectively, lowering the temperature at the contact point.
- Increased machining speed: Improved chip evacuation and cooling allow for higher feed rates and speeds, increasing productivity without sacrificing tool life.
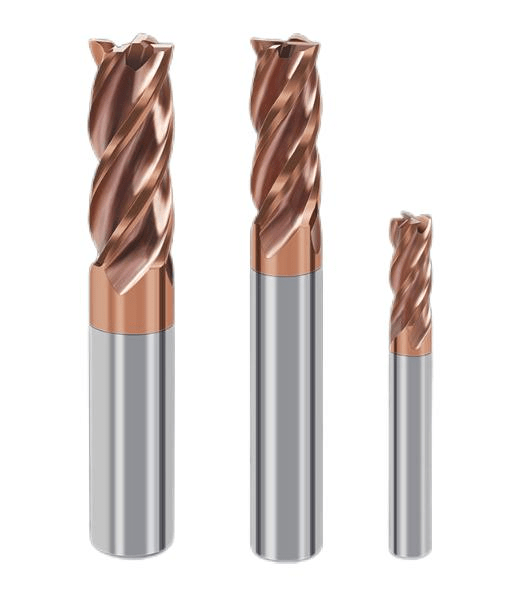
3. Multi-facet Cutting Edges
The cutting edge geometry of tungsten steel milling cutters has evolved with multi-faceted designs, where the edge has multiple facets instead of a single, sharp edge. These designs offer distinct advantages:
- Reduced cutting resistance: Multi-faceted edges distribute cutting forces across several points, lowering overall resistance and making the milling process more efficient.
- Improved tool stability: This design reduces the tendency of the tool to deflect under heavy loads, resulting in more precise machining.
- Enhanced durability: By distributing the force across multiple edges, the tool is less likely to suffer from edge breakage, leading to longer service life.
4. Application-specific Geometries
Certain industries require customized geometry features tailored to unique applications. Recent innovations have focused on specialized geometries for complex milling tasks:
- High-feed milling geometries: Designed with a specific geometry that allows for faster feed rates, these cutters remove material at a high speed without increasing the radial cutting force, ideal for large-volume material removal.
- Micro-milling geometries: For using tungsten steel milling cutter in precision micro-machining, especially in electronics or medical device manufacturing, tools with extremely fine cutting edges and optimized flute geometries enable high-precision cuts at small scales.
- Interrupted cut geometry: Used for materials like cast iron, this geometry handles interrupted cuts without causing excessive tool wear, making it highly durable for applications involving rough, interrupted surfaces.
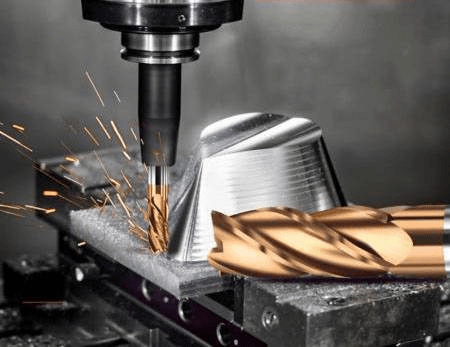
To sum up, Innovations in cutter geometries for tungsten steel milling cutters have driven remarkable advancements in machining efficiency, tool durability, and quality of the finished product. Through carefully selecting the cutter’s helix angle, flute design, corner configuration, edge geometry, etc, manufacturers can tailor these tools to meet specific material and application needs. Combined with advanced coatings, the latest geometrical designs allow tungsten steel cutters to perform optimally across various industrial applications.