The designs of screw threads have continuously evolved to meet modern engineering challenges. From increasing load capacity to improving vibration resistance, innovative screw thread designs are reshaping how industries address efficiency, reliability, and performance. This article focuses on some of the most notable advancements in the designs of screw threads and their applications.
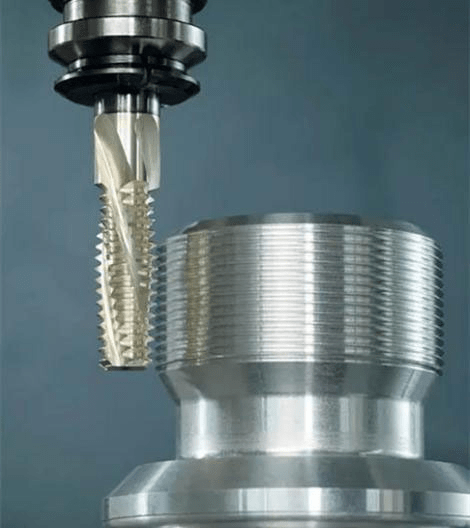
What are Screw Threads?
Screw threads are helical ridges or grooves wrapped around a cylindrical or conical surface. These threads allow fasteners, such as screws, bolts, and nuts, to engage with each other, enabling secure mechanical connections. They function by converting rotational motion into linear motion, or vice versa, depending on the design. Screw threads are classified based on their shape, pitch, and angle, and are essential in various applications, from simple household items to complex industrial machinery. They provide strong, reliable fastening, and are used for tasks ranging from simple assembly to transmitting power and motion.
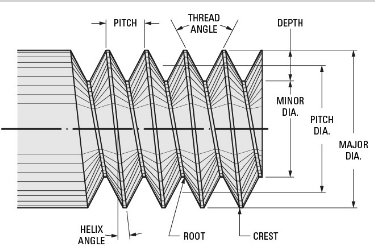
Common Traditional Design Types of Screw Threads
This chart highlights the most widely used traditional screw thread types, their defining features, and practical applications across various industries.
Thread Type | Description | Features | Common Applications |
V-Thread | A thread with a sharp, V-shaped profile. | High friction and good self-locking capability. | General-purpose fasteners, bolts, and screws. |
Square Thread | Features a square-shaped profile ideal for transmitting power. | High efficiency and low friction. | Lead screws in jacks, presses, and actuators. |
Acme Thread | Similar to square threads but with a trapezoidal profile for strength. | Greater load capacity and easier machining. | Lathe lead screws, heavy machinery. |
Buttress Thread | Designed with one steep flank and one shallow flank. | Handles high axial loads in one direction. | Hydraulic presses, oil rigs, and firearms. |
Knuckle Thread | Rounded crests and roots for better durability and resistance to damage. | Suitable for rough environments and easy cleaning. | Railway coupling systems, bottle caps. |
Whitworth Thread | A British standard thread with rounded crests and roots. | High durability and ease of production. | Plumbing, pipe connections, and vintage machinery. |
Unified Thread | A standard thread used across the US and Canada. | Offers interchangeability and standardization. | General fastening in industrial and consumer products. |
ISO Metric Thread | An international standard thread with a V-shaped profile. | Globally standardized, high reliability. | Automotive, construction, and electronics. |
Trapezoidal Thread | Similar to Acme but with more steeply angled flanks. | Handles higher loads with better wear resistance. | Power transmission in machine tools. |
Pipe Thread (NPT) | Tapered threads designed for sealing pipes. | Provides leak-proof connections. | Plumbing, gas fittings, and hydraulic systems. |
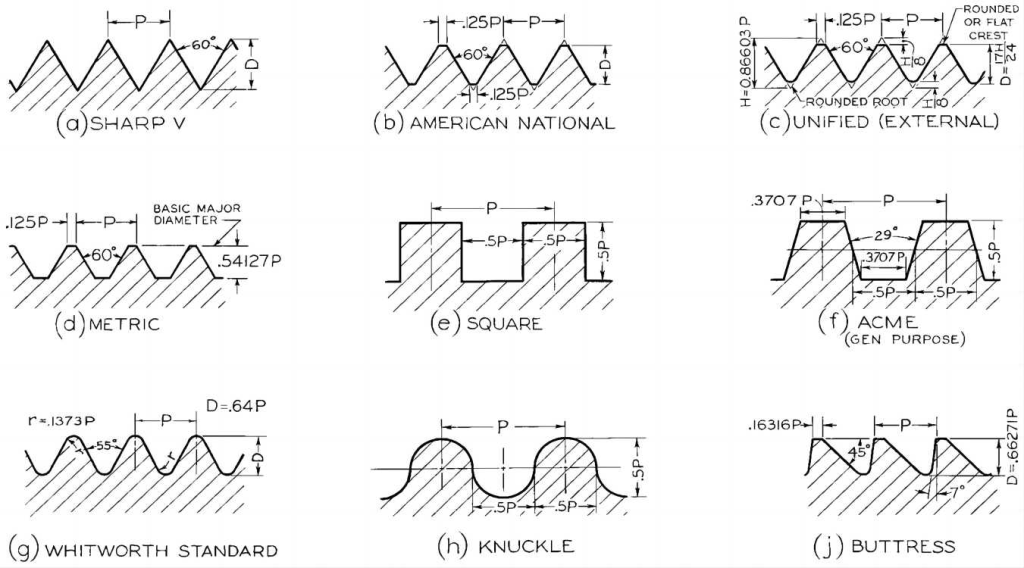
Key Advancements in Designs for Screw Threads
1. Self-Locking Threads
Self-locking threads feature unique geometries or additional components like nylon inserts to prevent unintentional loosening under vibration or dynamic loads. These threads reduce the need for additional screw thread locking mechanisms.
Advantages:
- Enhanced safety in critical applications.
- Improved assembly efficiency by eliminating external locking parts.
Applications:
Thread lock screws are ideal for aerospace, automotive engines, and heavy machinery.
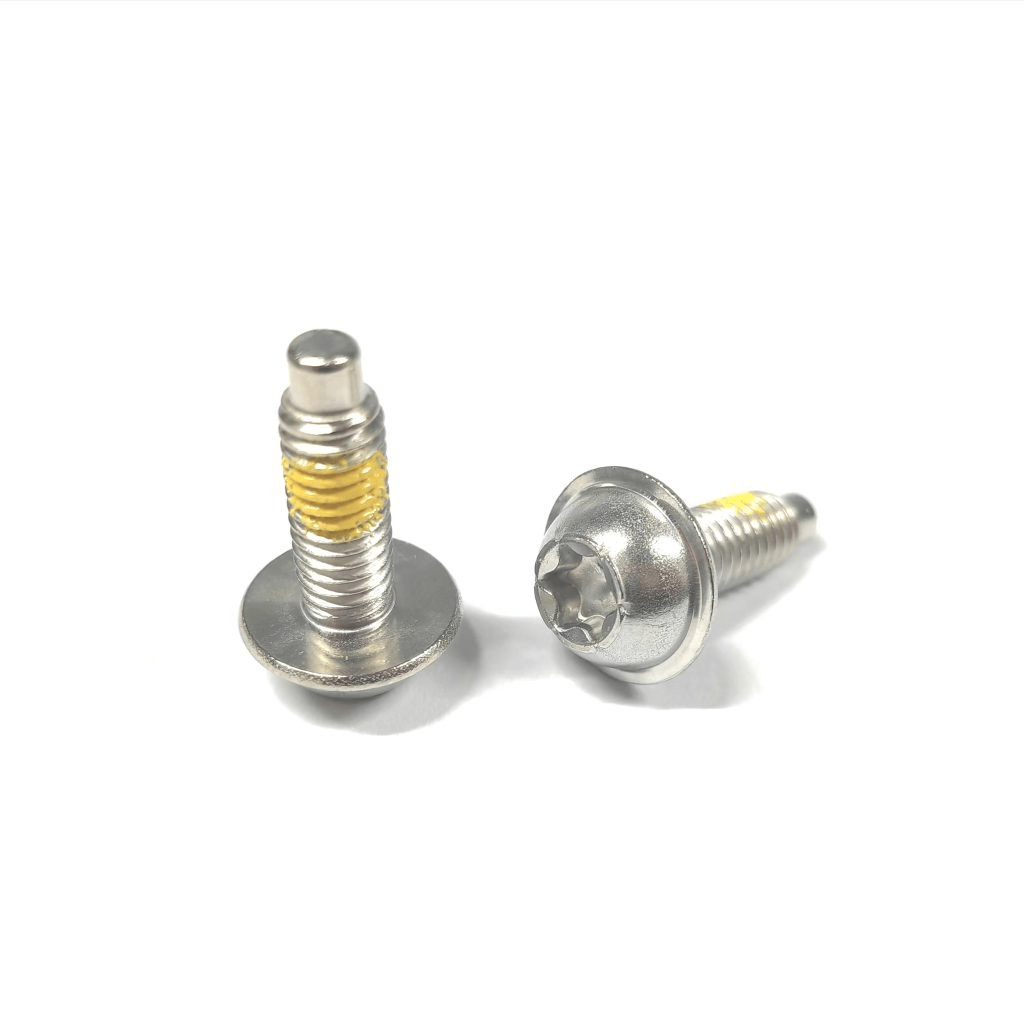
2. Dual-Lead Threads
Dual-lead threads consist of two intertwined thread profiles with different pitches, allowing for faster engagement and reduced rotation to achieve a tight fit. This design balances speed and precision.
Advantages:
- Accelerates fastening in repetitive tasks.
- Reduces worker fatigue during assembly.
Applications:
Packaging machinery, robotics, and assembly lines.
3. Variable-Pitch Threads
In this design, the pitch of the thread varies along its length. Such threads are used to create secure locking at specific points or allow controlled linear motion for specialized applications.
Advantages:
- Provides controlled engagement points.
- Offers high adjustability and precision.
Applications:
Medical devices, adjustable furniture, and robotics.
4. Waveform Threads
Waveform threads replace traditional straight profiles with undulating curves. This innovative design evenly distributes load and reduces stress concentrations.
Advantages:
- Increases thread durability.
- Reduces risk of cracking or thread deformation.
Applications:
High-load environments such as bridges and industrial presses.
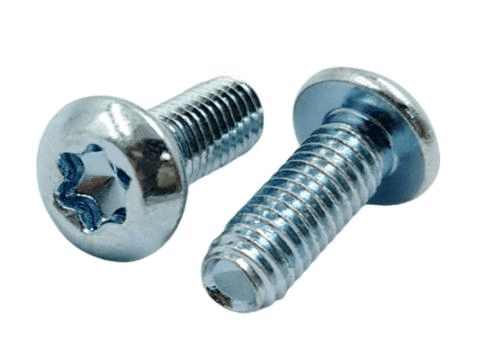
5. Buttress Threads with Optimized Angles
Traditional buttress threads are known for their strength under axial loads. Recent designs optimize the thread angle to handle higher forces while reducing material stress.
Advantages:
- Enhances load-bearing capacity.
- Offers superior resistance to force in one direction.
Applications:
Oil and gas rigs, hydraulic presses, and aerospace components.
6. Helicoidal and Tangential Threads
Helicoidal threads integrate tangential contact surfaces to improve the distribution of torque and load. These threads often include non-traditional geometries for precision applications.
Advantages:
- Enhances torque efficiency.
- Reduces material wear over time.
Applications:
Precision manufacturing, gear systems, and instrumentation.
7. Advanced Coatings for Extreme Conditions
Modern thread designs integrate advanced coatings that improve corrosion resistance, reduce friction, or add electrical conductivity. Examples include zinc-nickel plating, PTFE coatings, and ceramic treatments.
Advantages:
- Extends lifespan in harsh environments.
- Reduces maintenance and operational costs.
Applications:
Marine, electronics, and high-temperature machinery.
8. Micro-Threads for Miniature Applications
Micro-threads are finely designed threads for small-scale applications requiring high precision and strength in compact areas.
Advantages:
- Enables fastening in miniature devices.
- Offers reliable performance despite size constraints.
Applications:
Wearables, medical implants, and microelectronics.
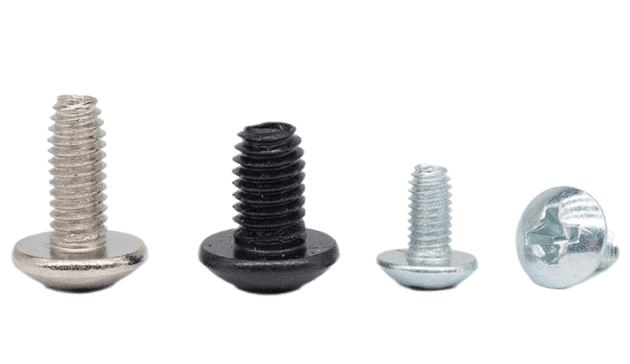
Key Considerations in Innovative Designs for Screw Threads
This chart outlines the critical factors for ensuring optimal performance, reliability, and applicability of innovative screw thread designs across industries.
Consideration | Description | Importance | Examples of Application |
Load Distribution | Ensuring even load across the thread surface to prevent stress concentration. | Increases durability and reduces wear. | Industrial presses, heavy machinery. |
Vibration Resistance | Designing threads to resist loosening under dynamic or vibrating conditions. | Enhances reliability in high-stress environments. | Aerospace, automotive engines. |
Material Compatibility | Selecting thread designs suited to the properties of the materials involved. | Prevents deformation or failure. | Medical devices, precision instruments. |
Ease of Assembly | Simplifying the fastening and unfastening process for efficiency. | Reduces time and labor costs. | Assembly lines, consumer electronics. |
Environmental Factors | Accounting for exposure to temperature, moisture, or corrosive conditions. | Extends operational lifespan. | Marine equipment, oil rigs. |
Thread Geometry | Optimizing profile shape (e.g., V-shape, trapezoidal, or curved). | Improves load capacity and application precision. | Robotics, lead screws. |
Innovative Coatings | Applying materials like PTFE or ceramic to enhance performance. | Reduces friction and prevents corrosion. | High-temperature machinery, marine applications. |
Customizability | Allowing for tailored designs for specific applications or industries. | Meets unique operational needs. | 3D-printed components, advanced manufacturing. |
Miniaturization | Designing micro-threads for compact and precise applications. | Expands use in small-scale technology. | Wearable tech, microelectronics. |
Sustainability | Using eco-friendly materials or designs to minimize environmental impact. | Promotes sustainable manufacturing practices. | Green construction, renewable energy systems. |
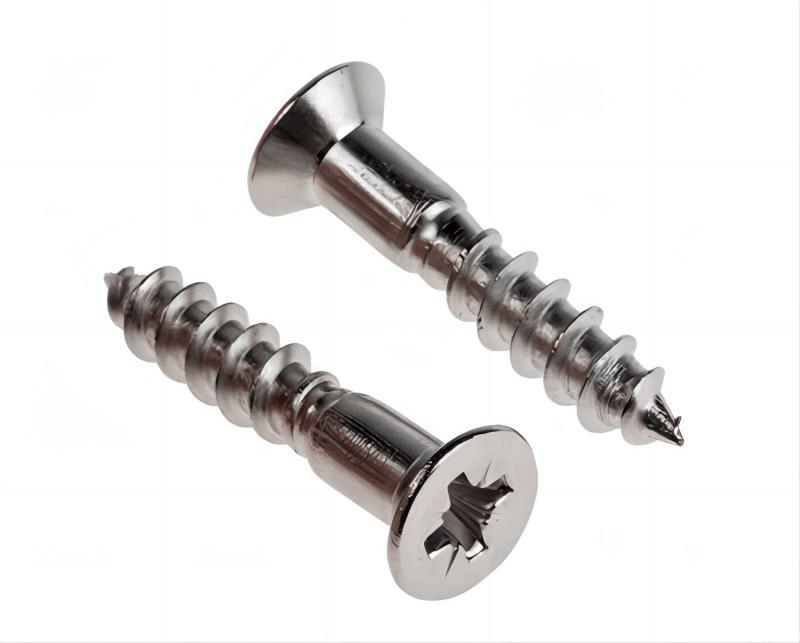
In summary, innovative designs in screw threads are addressing the ever-growing demands of industries by enhancing functionality, durability, and efficiency. These advancements not only solve traditional challenges but also open up new possibilities for applications in precision engineering, robotics, and more.